AUVESY-MDT
We secure the world's automation
HQ Location
Germany
|
Year Founded
2007
|
Company Type
Private
|
Revenue
$10-100m
|
Employees
51 - 200
|
Website
|
Twitter Handle
|
AUVESY-MDT is a solid medium-sized enterprise based in Rhineland-Palatinate, Germany. The software octoplant offers worldwide a secure solution for version control and data management in industrial automation. This leading version control software is the basis to heighten production efficiency by reducing errors and downtime; and monitor and control automation projects.
傲晖数据软件(南京)有限公司是AUVESY-MDT在中国的全资子公司,与西门子、施耐德、三菱、微软等合作伙伴携手已为全球50多个国家安装3200多套软件。AUVESY-MDT研发的versiondog/octoplant用来统一管理各种自动化设备(如:PLC/机器人/HMI/CNC/相机/压机/拧紧机/工控机/马达驱动等),且不受制造商的限制,实现灾难恢复以提高运营效率,并减轻网络安全攻击,保持生产连续不间断。集团总部位于德国兰道。
When AUVESY-MDT talks about the Internet of Things (IoT), they are not just talking about smart factories, but also smart products. The combination of the two means that the production of small batches and one-off products becomes practical even in highly automated facilities. versiondog is the certified enterprise solution for software and data management in the automated production. With versiondog, customers can make automated backups of their data and at the same time have a powerful versioning system for project data and documentation, including integrated lifecycle management. versiondog interprets data and programs of the different automated components and automates the administration of the flood of data and versions, which accrues in every production. versiondog does not only administrate all this project data but controls, analyses and monitors all changes in the devices and that automatically. The current producing program, the used parameters and set points as well as the clear version allocation are available at any time.
octoplant是AUVESY-MDT研发的一款用于自动化生产中程序备份和版本管理的企业级解决方案,统一管理各种自动化设备(如:PLC、DCS、SCADA、机器人、HMI、CNC、相机、压机、拧紧枪、工控机、交换机、路由器、防护墙、马达驱动等),通过对设备控制系统程序、参数进行自动备份、版本管理和软件状态记录、BI展示分析,确保制造过程的可视化、完全可追溯性且不受原制造商的限制,实现快速灾难恢复以提高运营效率,并减轻网络安全攻击,保持生产连续不间断。
Octoplant创新性地为工厂层的生产设施设备提供了一个中央数据管理系统,只需点击一个按钮,即可保护您的数据、质量证明、项目文档和变更管理。
Tesla, Space-X, CERN, Daimler, GM, Ford, BMW, Audi, Volkswagen, Volvo, Porsche, Bosch, Continental, Mann & Hummel, ZF, Brose, Nestle, Coca Cola, Kraftfood, Mars, Airbus, Benteler, Eisenmann, Dürr, Roche, Boehringer Ingelheim, Fresenius, Sun Chemical, RWE, Vattenfall
-
Devices Layer
-
Edge Layer
-
Cloud Layer
-
Application Layer
-
Supporting Technologies
Supplier missing?
Start adding your own!
Register with your work email and create a new supplier profile for your business.
Case Studies.








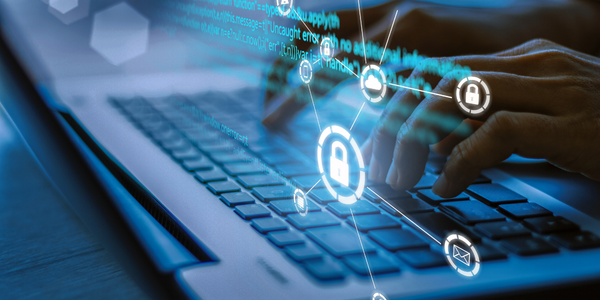

Similar Suppliers.



Partners.

---nyse--ge_1.jpg)







