Technology Category
- Analytics & Modeling - Digital Twin / Simulation
Applicable Industries
- Railway & Metro
- Transportation
Applicable Functions
- Product Research & Development
- Quality Assurance
Use Cases
- Manufacturing Process Simulation
- Transportation Simulation
Services
- Hardware Design & Engineering Services
- Testing & Certification
About The Customer
BNSF Logistics LLC is a registered engineering firm that specializes in railcar design, stress analysis, wind turbine blade transport, and cargo securement. With over 100 collective years of experience in the rail industry, BNSFL is a trusted name in the field. They are known for their innovative solutions and commitment to delivering high-quality services to their clients. In this case, a new customer approached BNSFL with a request for a stress analysis on their covered hopper design. When it was determined that significant structural changes were needed to meet industry standards, the customer expanded the scope of work to include both the modified CAD design and supporting stress analysis.
The Challenge
In the rail industry, hardware testing is a costly and time-consuming process, often limited to research and development at the Masters and Ph.D. levels. This level of detail is often unnecessary and cost-prohibitive for typical railcar manufacturing. However, as more railcars are phased out due to service age, there is a growing demand for new railcar designs. Freight transit by railcar is favored by many companies due to its low cost per high volume shipment. A new customer of BNSF Logistics LLC (BNSFL) requested a stress analysis on their covered hopper design. When it became clear that significant structural changes would be needed to meet the Association of American Railroads (AAR) requirements, the customer requested a larger scope of work beyond FEA verification. BNSFL was then tasked to deliver both the modified CAD design and supporting stress analysis. The success of the project depended on simulation to demonstrate the railcar’s structural integrity.
The Solution
BNSFL, in collaboration with ANSYS, was able to deliver a reliable railcar design to the customer. ANSYS was specifically chosen as the simulation solution for its ease of model integration from other CAD software, advanced features for linear and nonlinear analysis, reliability in precision and accuracy, and its industry reputation as a leader in structural simulation. ANSYS provided a reliable way of receiving stress feedback from the original CAD model, allowing a quick turnaround process. This helped deliver an on-time drawing package to the customer and presented an alternative means of verification that is significantly more cost-effective than traditional hardware testing.
Operational Impact
Case Study missing?
Start adding your own!
Register with your work email and create a new case study profile for your business.
Related Case Studies.
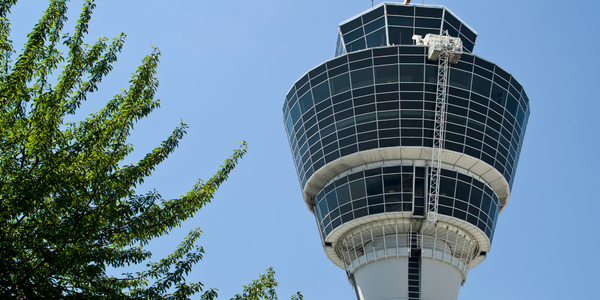
Case Study
Airport SCADA Systems Improve Service Levels
Modern airports are one of the busiest environments on Earth and rely on process automation equipment to ensure service operators achieve their KPIs. Increasingly airport SCADA systems are being used to control all aspects of the operation and associated facilities. This is because unplanned system downtime can cost dearly, both in terms of reduced revenues and the associated loss of customer satisfaction due to inevitable travel inconvenience and disruption.
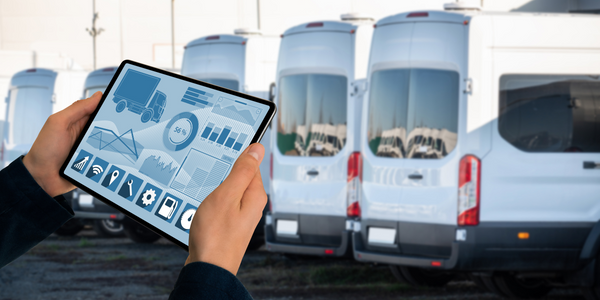
Case Study
IoT-based Fleet Intelligence Innovation
Speed to market is precious for DRVR, a rapidly growing start-up company. With a business model dependent on reliable mobile data, managers were spending their lives trying to negotiate data roaming deals with mobile network operators in different countries. And, even then, service quality was a constant concern.
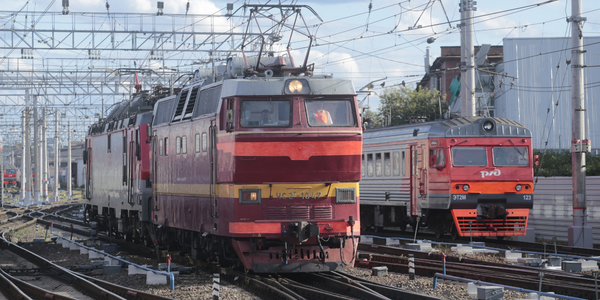
Case Study
Digitize Railway with Deutsche Bahn
To reduce maintenance costs and delay-causing failures for Deutsche Bahn. They need manual measurements by a position measurement system based on custom-made MEMS sensor clusters, which allow autonomous and continuous monitoring with wireless data transmission and long battery. They were looking for data pre-processing solution in the sensor and machine learning algorithms in the cloud so as to detect critical wear.
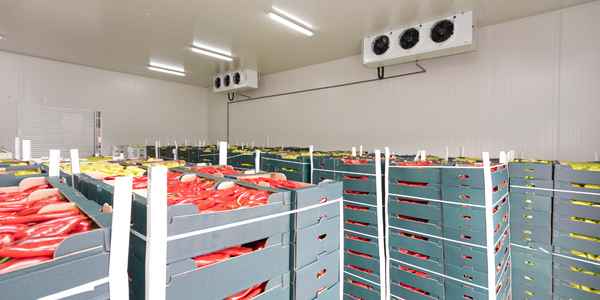
Case Study
Cold Chain Transportation and Refrigerated Fleet Management System
1) Create a digital connected transportation solution to retrofit cold chain trailers with real-time tracking and controls. 2) Prevent multi-million dollar losses due to theft or spoilage. 3) Deliver a digital chain-of-custody solution for door to door load monitoring and security. 4) Provide a trusted multi-fleet solution in a single application with granular data and access controls.
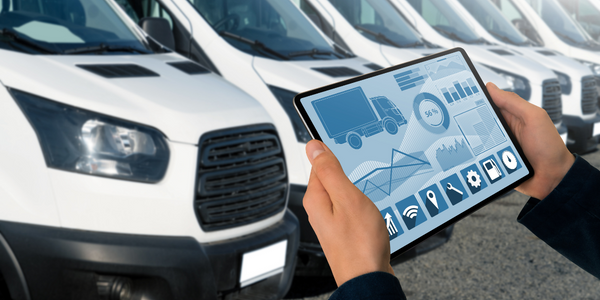
Case Study
Vehicle Fleet Analytics
Organizations frequently implement a maintenance strategy for their fleets of vehicles using a combination of time and usage based maintenance schedules. While effective as a whole, time and usage based schedules do not take into account driving patterns, environmental factors, and sensors currently deployed within the vehicle measuring crank voltage, ignition voltage, and acceleration, all of which have a significant influence on the overall health of the vehicle.In a typical fleet, a large percentage of road calls are related to electrical failure, with battery failure being a common cause. Battery failures result in unmet service agreement levels and costly re-adjustment of scheduled to provide replacement vehicles. To reduce the impact of unplanned maintenance, the transportation logistics company was interested in a trial of C3 Vehicle Fleet Analytics.
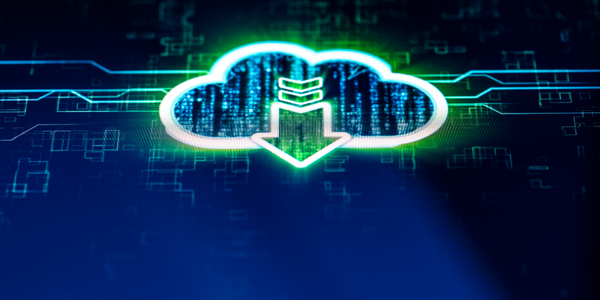
Case Study
3M Gains Real-Time Insight with Cloud Solution
The company has a long track record of innovative technology solutions. For example, 3M helps its customers optimize parking operations by automating fee collection and other processes. To improve support for this rapidly expanding segment, 3M needed to automate its own data collection and reporting. The company had recently purchased the assets of parking, tolling, and automatic license plate reader businesses, and required better insight into these acquisitions. Chad Reed, Global Business Manager for 3M Parking Systems, says, “With thousands of installations across the world, we couldn’t keep track of our software and hardware deployments, which made it difficult to understand our market penetration.” 3M wanted a tracking application that sales staff could use to get real-time information about the type and location of 3M products in parking lots and garages. So that it could be used on-site with potential customers, the solution would have to provide access to data anytime, anywhere, and from an array of mobile devices. Jason Fox, Mobile Application Architect at 3M, upped the ante by volunteering to deliver the new app in one weekend. For Fox and his team, these requirements meant turning to the cloud instead of an on-premises datacenter. “My first thought was to go directly to the cloud because we needed to provide access not only to our salespeople, but to resellers who didn’t have access to our internal network,” says Fox. “The cloud just seemed like a logical choice.”