Technology Category
- Cybersecurity & Privacy - Identity & Authentication Management
- Networks & Connectivity - RFID
Applicable Industries
- Marine & Shipping
- Transportation
Applicable Functions
- Product Research & Development
Use Cases
- Structural Health Monitoring
About The Customer
The Aircraft Carrier Alliance (ACA) is a unique partnering relationship between industry leaders in the UK's aerospace and defense sectors. The ACA is responsible for delivering the Queen Elizabeth Class aircraft carriers, the largest warships ever built in the UK. The alliance is made up of BAE Systems, Babcock, Thales, and the UK Ministry of Defence. The ACA is committed to delivering a first-class naval capability to the UK's Royal Navy, and as such, they are constantly seeking innovative solutions to improve the design and manufacturing processes of their naval vessels.
The Challenge
The Aircraft Carrier Alliance (ACA) faced a significant challenge in the concept and preliminary design phases of a naval ship project. The designers were often required to work with limited data on the major structural design drivers for the vessel. This often led to a largely subjective design approach, which could result in inefficiency and even structural problems being locked-in from the start. To rectify any issues, increased material use, weight, and unnecessary complexity, as well as high design and manufacture costs, could be introduced to the end product. The ACA sought to evaluate the potential of simulation-driven design under the unique requirements of naval ship design.
The Solution
The ACA partnered with Altair ProductDesign to apply optimization technology to drive efficient, right first time design solutions to a series of structural regions of the vessel. One area of interest was the aircraft carrier’s flight control (FLYCO) module. The FLYCO module structure is comprised of a large glazed area supported between an upper and lower sponson structures. These sponson structures are required to meet natural frequency and deflection targets and are therefore subject to the complex interactions of mass and stiffness. Topology optimization was first employed to identify the optimum global positioning of stiffening webs within the package envelope of the module. This was followed by a further round of topology optimization to identify the optimum load paths within those webs, such that openings could be cut without compromising structural performance. Finally, size and shape optimization was employed to fine-tune the plate thicknesses and opening sizes to minimize mass and design complexity while meeting design targets.
Operational Impact
Quantitative Benefit
Case Study missing?
Start adding your own!
Register with your work email and create a new case study profile for your business.
Related Case Studies.
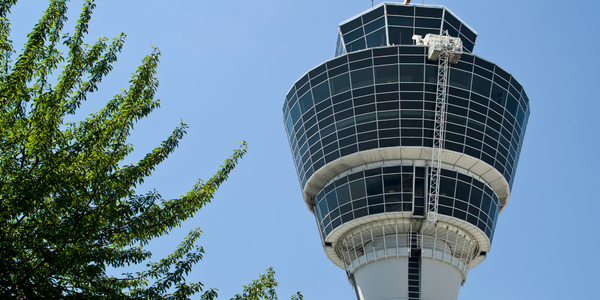
Case Study
Airport SCADA Systems Improve Service Levels
Modern airports are one of the busiest environments on Earth and rely on process automation equipment to ensure service operators achieve their KPIs. Increasingly airport SCADA systems are being used to control all aspects of the operation and associated facilities. This is because unplanned system downtime can cost dearly, both in terms of reduced revenues and the associated loss of customer satisfaction due to inevitable travel inconvenience and disruption.
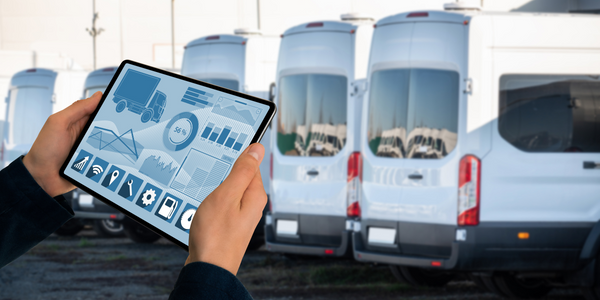
Case Study
IoT-based Fleet Intelligence Innovation
Speed to market is precious for DRVR, a rapidly growing start-up company. With a business model dependent on reliable mobile data, managers were spending their lives trying to negotiate data roaming deals with mobile network operators in different countries. And, even then, service quality was a constant concern.
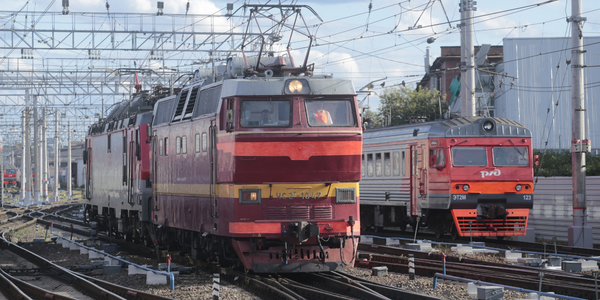
Case Study
Digitize Railway with Deutsche Bahn
To reduce maintenance costs and delay-causing failures for Deutsche Bahn. They need manual measurements by a position measurement system based on custom-made MEMS sensor clusters, which allow autonomous and continuous monitoring with wireless data transmission and long battery. They were looking for data pre-processing solution in the sensor and machine learning algorithms in the cloud so as to detect critical wear.
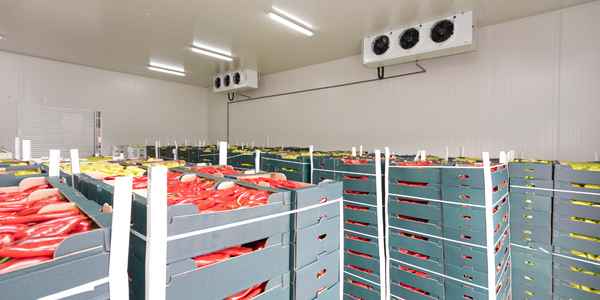
Case Study
Cold Chain Transportation and Refrigerated Fleet Management System
1) Create a digital connected transportation solution to retrofit cold chain trailers with real-time tracking and controls. 2) Prevent multi-million dollar losses due to theft or spoilage. 3) Deliver a digital chain-of-custody solution for door to door load monitoring and security. 4) Provide a trusted multi-fleet solution in a single application with granular data and access controls.
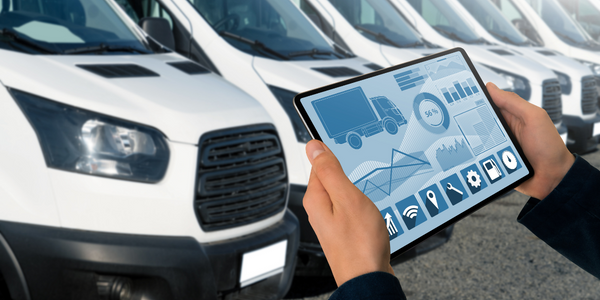
Case Study
Vehicle Fleet Analytics
Organizations frequently implement a maintenance strategy for their fleets of vehicles using a combination of time and usage based maintenance schedules. While effective as a whole, time and usage based schedules do not take into account driving patterns, environmental factors, and sensors currently deployed within the vehicle measuring crank voltage, ignition voltage, and acceleration, all of which have a significant influence on the overall health of the vehicle.In a typical fleet, a large percentage of road calls are related to electrical failure, with battery failure being a common cause. Battery failures result in unmet service agreement levels and costly re-adjustment of scheduled to provide replacement vehicles. To reduce the impact of unplanned maintenance, the transportation logistics company was interested in a trial of C3 Vehicle Fleet Analytics.
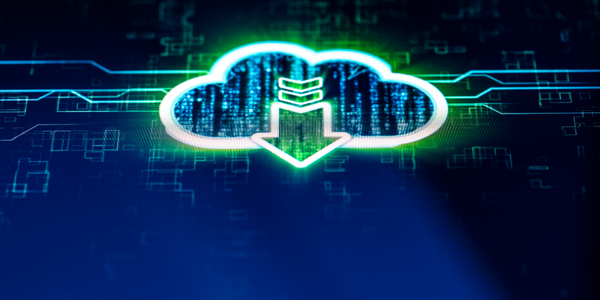
Case Study
3M Gains Real-Time Insight with Cloud Solution
The company has a long track record of innovative technology solutions. For example, 3M helps its customers optimize parking operations by automating fee collection and other processes. To improve support for this rapidly expanding segment, 3M needed to automate its own data collection and reporting. The company had recently purchased the assets of parking, tolling, and automatic license plate reader businesses, and required better insight into these acquisitions. Chad Reed, Global Business Manager for 3M Parking Systems, says, “With thousands of installations across the world, we couldn’t keep track of our software and hardware deployments, which made it difficult to understand our market penetration.” 3M wanted a tracking application that sales staff could use to get real-time information about the type and location of 3M products in parking lots and garages. So that it could be used on-site with potential customers, the solution would have to provide access to data anytime, anywhere, and from an array of mobile devices. Jason Fox, Mobile Application Architect at 3M, upped the ante by volunteering to deliver the new app in one weekend. For Fox and his team, these requirements meant turning to the cloud instead of an on-premises datacenter. “My first thought was to go directly to the cloud because we needed to provide access not only to our salespeople, but to resellers who didn’t have access to our internal network,” says Fox. “The cloud just seemed like a logical choice.”